Maintenance and Repairs of Offshore Platforms
Maintaining offshore structures is a complex and challenging task that involves a range of strategies to ensure the safety, reliability, and longevity of the structures. Offshore platforms and structures such as oil rigs, wind farms, and subsea pipelines operate in a harsh and dynamic marine environment, which can significantly affect their condition over time. Below is a detailed overview of the strategies for maintaining offshore structures, the challenges involved, and the best practices used in the industry.
1. Types of Offshore Structures
Offshore structures vary in design and function. The main types of offshore structures include:
- Fixed platforms: These are anchored to the seabed using large concrete or steel structures, typically used for oil and gas production.
- Floating platforms (FPSOs and semi-submersibles): These are floating units anchored to the seabed, often used in deeper waters.
- Subsea structures: Includes subsea pipelines, manifolds, and wellheads.
- Offshore wind farms: These include wind turbines installed at sea, either on fixed or floating foundations.
2. Key Maintenance Strategies
To ensure the continued functionality of offshore structures, a variety of maintenance strategies are employed. These can be broadly categorized into:
A. Preventive Maintenance (PM)
Preventive maintenance involves regular inspections, servicing, and component replacements to avoid equipment failure. Key aspects include:
- Scheduled inspections: Regularly checking the condition of critical systems, such as structural integrity, electrical systems, safety equipment, and communication systems.
- Corrosion protection: Applying coatings, cathodic protection systems (CP), and corrosion inhibitors to prevent damage from saltwater and other environmental factors.
- Lubrication and fluid checks: Regular maintenance of moving parts like cranes, turbines, and pumps, ensuring they are properly lubricated and functioning.
- Calibration and testing: Ensuring all systems are calibrated to operate within their specified tolerances, such as pressure, temperature, and flow sensors.
- Spare parts inventory: Maintaining an inventory of critical spare parts to minimize downtime during failures.
B. Predictive Maintenance (PdM)
Predictive maintenance uses advanced data analysis and real-time monitoring to predict when failures might occur. This strategy relies on:
- Condition monitoring: Using sensors and monitoring equipment to track key parameters such as vibration, temperature, pressure, and acoustic emissions to detect early signs of malfunction or wear.
- Machine learning algorithms: Advanced data analytics and AI are increasingly being used to predict maintenance needs by analyzing trends in operational data.
- Remote monitoring: Offshore structures are equipped with sensors that provide real-time data to onshore facilities, allowing experts to monitor the health of assets and predict potential failures.
C. Corrective Maintenance
Corrective maintenance involves repairing or replacing equipment after it has failed. While this strategy is often reactive, it is still necessary for dealing with unforeseen failures that can’t be predicted or prevented.
- Emergency repair protocols: Ensuring that there are clear plans for responding to major failures, including having repair teams on standby, and maintaining equipment on site to address urgent needs.
- Mobilization of repair teams: Quick mobilization of skilled personnel, specialized equipment, and resources to address critical failures, especially in remote offshore locations.
D. Structural Integrity Management
Ensuring the structural integrity of offshore platforms and subsea pipelines is a top priority. This involves:
- Regular structural inspections: These may include visual inspections, non-destructive testing (NDT) methods like ultrasonic testing, radiography, and magnetic particle inspection.
- Jack-up rigs and other mobile platforms: These structures may require additional checks on the stability of their legs, the condition of buoyancy tanks, and the structural frame.
- Fatigue analysis and load testing: Evaluating the impacts of long-term fatigue from waves, wind, and other forces on the structure’s components. This also involves ensuring that the structure can handle the weight of equipment and personnel.
E. Environmental Monitoring and Maintenance
The offshore environment is dynamic and can lead to various challenges. The maintenance of offshore structures must account for:
- Weather and sea conditions: Extreme weather events, such as hurricanes or heavy storms, can lead to structural damage, equipment failure, or safety risks. Maintenance teams need to prepare for and react quickly to these events.
- Marine life and biofouling: Marine organisms can grow on underwater structures, affecting their performance and leading to corrosion. Regular cleaning and anti-fouling coatings are used to address this.
- Wave and tidal forces: The effects of wave action and tidal movements can wear down materials, requiring regular inspection and reinforcement of key structural components.
3. Challenges in Offshore Structure Maintenance
Despite the advanced maintenance strategies, several challenges make offshore structure maintenance difficult:
A. Harsh and Unpredictable Environmental Conditions
- Weather and Sea States: Offshore structures are exposed to dynamic forces such as waves, wind, and storms, making maintenance challenging. Operations can often be halted due to poor weather conditions, and specialized equipment is needed to withstand such forces.
- Corrosion: The saline environment accelerates corrosion of metal components, especially in subsea environments. Maintaining and replacing corroded parts is a constant concern.
- Temperature Extremes: Offshore structures often experience extreme temperature variations, which can affect both materials and equipment.
B. Remote and Inaccessible Locations
- Logistical Challenges: Offshore structures are often located in remote areas far from shore, making transportation of personnel, equipment, and supplies a logistical challenge. Special vessels or helicopters are often needed to mobilize personnel and materials, increasing costs and complexity.
- Limited Access for Repairs: In some cases, offshore platforms and subsea pipelines are not easily accessible, which complicates routine maintenance and emergency repairs.
C. High Costs
- Expensive Equipment and Tools: Offshore operations require specialized, expensive equipment for inspection, repair, and replacement of parts, which increases operational costs.
- Personnel Costs: Skilled personnel, such as divers or engineers, must be flown in and out of offshore locations, further increasing labor costs.
- Downtime Costs: Any downtime or delayed maintenance can lead to significant financial losses due to lost production, downtime fees, or regulatory fines.
D. Safety Concerns
- Risk of Accidents: Offshore environments can be hazardous, with risks such as explosions, falls, and equipment failure. Rigorous safety procedures are necessary to protect personnel, but maintaining safety standards in the face of challenging environments is a continual concern.
- Handling Hazardous Materials: Offshore structures often deal with oil, gas, and chemicals, which present risks of spills, leaks, and exposure. Handling these substances safely requires specialized equipment and training.
E. Technological Limitations
- Inspection Technologies: While technologies like drones, remotely operated vehicles (ROVs), and AI-assisted analytics have improved, there are still limitations in their ability to perform complex inspections or handle challenging environments like deep-sea exploration or highly corrosive areas.
- Aging Infrastructure: Many offshore structures, particularly those built decades ago, have aging infrastructure that can be difficult to upgrade or maintain without substantial investments.
4. Best Practices for Overcoming Challenges
- Regular Training and Safety Drills: To mitigate safety risks, regular training sessions and emergency drills are essential for the crew. This ensures they are prepared to act quickly in case of accidents.
- Collaborative Partnerships: Many companies partner with specialized maintenance providers or third-party experts to ensure the maintenance is performed efficiently and effectively.
- Technological Advancements: Embracing new technologies like AI, drones, ROVs, and real-time data analytics can help predict failures and automate inspection and maintenance processes, reducing both human error and operational costs.
- Optimized Maintenance Scheduling: Using advanced software for predictive maintenance can help optimize the scheduling of repairs and inspections, preventing downtime and reducing costs.
- Enhanced Environmental Protection: Installing more effective anti-corrosion coatings, biofouling-resistant materials, and automated cleaning systems can mitigate environmental challenges.
Conclusion
Maintaining offshore structures requires a comprehensive, multi-faceted approach that combines regular inspections, predictive analytics, and advanced technology. However, the challenges posed by the harsh marine environment, remote locations, high costs, and safety concerns make it a demanding field. By employing effective strategies and embracing technological innovations, offshore operators can extend the life of their structures, enhance safety, and reduce costs over time.
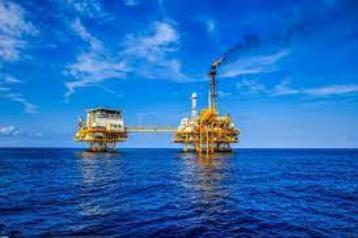